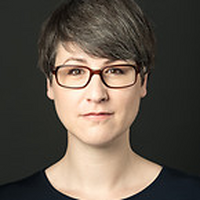
Monique Opetz
München
-
Noch keine BeiträgeHier wird noch geschrieben ... bitte schaue bald nochmal vorbei
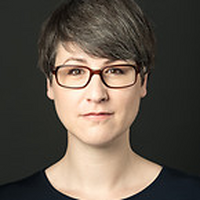
Monique Opetz
-
maschinenbau
-
technik
-
wissenschaft
-
digitalisierung
-
robotik
-
internet of things
-
industrie 4.0
-
neue technologien
-
innovationen
-
life sciences
Kurzbio
Seit 2011 ich schreibe als freie Journalistin und Autorin über Digitalisierung im Alltag und in den Fabrikhallen. Dafür erkunde ich Makerspaces, Werkshallen oder Forschungslabore und spreche mit den Menschen hinter den Technologien. So entstehen Geschichten über softe Roboter, Turnschuhe in Losgröße 1 oder WLAN-Richtfunkantennen aus Chipsdosen – die in (Kunden-)Zeitschriften, auf Corporate Blogs oder in anderen Publikationen zu lesen sind.
---------
Monique Opetz (*1980) arbeitet als freie Journalistin und Social Media Managerin in München, u.a. für den VDMA, Dataport, die Verlagsgruppe Random House oder das Technikmagazin CHIP. Sie studierte Germanistik/ Anglistik an der Universität Stuttgart und absolvierte ihre journalistische Ausbildung während eines klassischen Zeitschriften-Volontariats.
Auftraggeber
Data(re)port - Digitales für Menschen , FERCHAUaktuell - Das Magazin für Engineering und IT , M-Plan , Technikmagazin CHIP , Verband Deutscher Maschinen- und Anlagenbau , Verlagsgruppe Random House
Fehler!
Leider konnte der Artikel nicht gefunden werden.
We can't find the internet
Attempting to reconnect
Something went wrong!
Hang in there while we get back on track