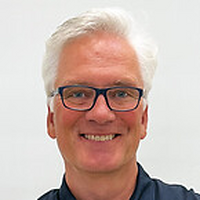
Dirk Kunde
Hamburg
-
Noch keine BeiträgeHier wird noch geschrieben ... bitte schaue bald nochmal vorbei
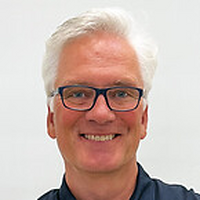
Dirk Kunde
-
automobilindustrie
-
autonomes fahren
-
elektromobilität
-
e-autos
Diplom-Volkswirt mit einem Faible für Technik. Spezialisierung auf Elektromobilität: E-Autos, Autonomes Fahren und Sektorkopplung mit der Energiewirtschaft.
Auftraggeber
Golem.de , Next Mobility , c´t
Weitere Profile
Fehler!
Leider konnte der Artikel nicht gefunden werden.
We can't find the internet
Attempting to reconnect
Something went wrong!
Hang in there while we get back on track