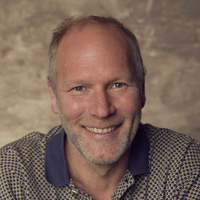
Daniel Hautmann
Hamburg
-
Noch keine BeiträgeHier wird noch geschrieben ... bitte schaue bald nochmal vorbei
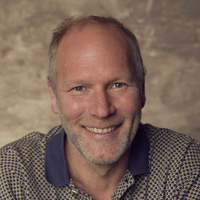
Daniel Hautmann
Spezialist für Technik-Texte: Ausbildung zum Industriemechaniker und zum Fachzeitschriftenredakteur.
Ich schreibe für Magazine und Tageszeitungen, zudem für Agenturen, Corporate-Publishing-Titel und Unternehmen. Daraus mache ich kein Geheimnis - alle Kunden veröffentliche ich auf meiner website!
Technik/Energie/Umwelt, das beschreibt am besten, was ich so mache. Meine Themenwelt dreht sich um regenerative Energien, Umwelt, Schifffahrt und alles, was mit Sport und Technik zu tun hat.
Ich bin Autor des Fachbuchs "Windkraft neu gedacht: Erstaunliche Beispiele für die Nutzung einer unerschöpflichen Ressource", 2021 bei Hanser Verlag erschienen.
Im Juli 2025 habe ich den UMSICHT-Wissenschaftspreis gewonnen.
Ich moderiere gerne Veranstaltungen oder leite Barcamps. Zudem gebe ich Pressetrainings und bin als Ghostwriter aktiv. Gelegentlich arbeite ich auch fürs Radio und vor der Kamera.
Mit dem von mir mitgegründeten Audio-Label "Honig & Gold" produzieren wir opulente Hörspiele, Podcasts, Audio-Spaziergänge und Live-Events: www.honigundgold.de
Beauftragen & Kontaktieren: [email protected]
Auftraggeber
Brand Eins , EnergieWinde , FAZ , Focus , GEO , Golem , NZZ , P. M. Magazin , Technology Review
Weitere Profile
Audio-Label: Honig & Gold , Author Central , Daniel Hautmann , Freischreiber , Hanser Fachbuch , Linked In , xing
Fehler!
Leider konnte der Artikel nicht gefunden werden.
We can't find the internet
Attempting to reconnect
Something went wrong!
Hang in there while we get back on track