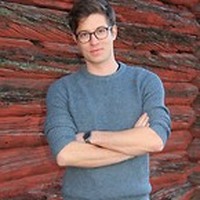
Bernd Eberhart
-
Noch keine BeiträgeHier wird noch geschrieben ... bitte schaue bald nochmal vorbei
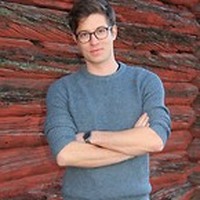
Bernd Eberhart
-
artenschutz
-
biologie
-
umwelt
-
wissenschaft
-
ökologie
-
neurologie
-
sprachwissenschaft
Auszeichnungen und Stipendien
Nominiert für den Georg von Holtzbrinck Preis für Wissenschaftsjournalismus 2023
Shortlist für den Egon Erwin Kisch-Preis 2023: "Gefährliche Botschaften", erschienen im Zeitmagazin Nr. 27/2022
Nominiert für den Deutschen Reporterpreis 2018 in der Kategorie Wissenschaftsreportage: "Der Biostaat", brand eins 4/2018
Media-Ambassadors India-Germany, Fellow 2017 (http://india.medienbotschafter.com/en/fellows/fellows/)
Lehrtätigkeit
Universität Tübingen: Praxisseminare Wissenschaftsjournalismus
(Studium Professionale, Career Service, Seminar für Allgemeine Rhetorik)
Reportageschule Reutlingen: Die Wissenschaftsreportage
Auftraggeber
Badische Zeitung , Bild der Wissenschaft , Brigitte , Der Tagesspiegel , GEO , GEOlino , PM History , Rheinpfalz am Sonntag , Science Notes Magazin , Stuttgarter Zeitung , Süddeutsche Zeitung , Tages Anzeiger , The Wire , ZEIT , Zeitmagazin , brand eins
Fehler!
Leider konnte der Artikel nicht gefunden werden.
We can't find the internet
Attempting to reconnect
Something went wrong!
Hang in there while we get back on track